Reduce dust pollution with secured transfer points
Many production plants struggle with excessive dust, leading to serious operational challenges. When bulk material is transported through the facility, it often spills over, affecting the entire working environment. Over time, conveyor belts and surrounding equipment get coated in fine dust, which can impact production efficiency and even pose fire and explosion risks.
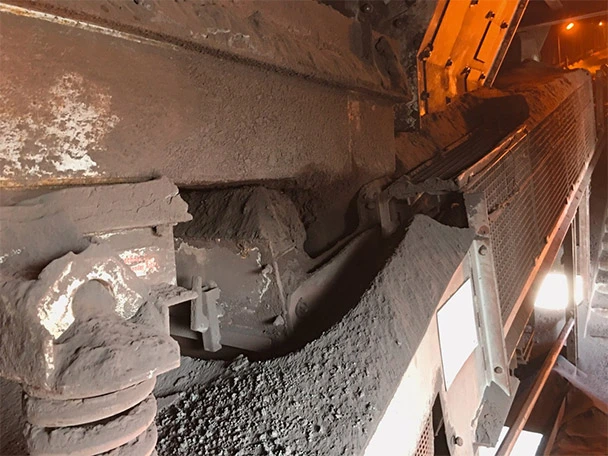
Bulk material being conveyed from one end of the production to the other quickly spills over
To manage this, companies often take the simplest approach - continuous cleaning (Fig. 2). A staff member is assigned to sweep, vacuum, or blow away the dust, even though it shouldn't have spread in the first place. This method, however, only provides a temporary fix. Once dust is in the air, it travels through production, settling into even the smallest places. Many workers use compressed air to remove dust from hard-to-reach places, which only worsens the problem by spreading it further and creating safety hazards.
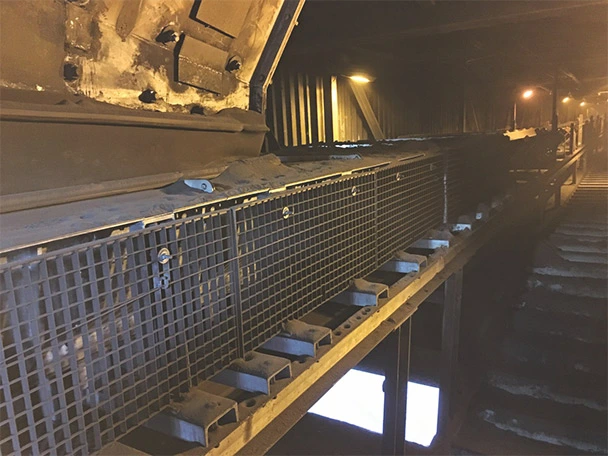
Often everything then needs to be cleaned manually
To protect employees handling the cleanup, companies enforce strict safety measures. This means full personal protective equipment (PPE): disposable suits, goggles, masks, gloves, and shoe covers. However, the cleaning process is time-consuming and repetitive, often done alongside regular duties. Rushing the task can create even more airborne dust, making the problem worse. Some companies go as far as implementing dedicated “cleaning shifts,” where employees suit up to clean together. If separate cleaning shifts aren't possible, companies may require all workers to wear PPE throughout the day, increasing costs and reducing efficiency.
Beyond the health risks, these cleaning efforts are expensive. The cost of PPE, cleaning supplies, additional staff, and equipment wear and tear adds up quickly. Frequent maintenance is needed, and moving parts wear out faster, requiring regular replacement.
A Smarter Approach: Fixing the Root Cause
A simple rule in quality management states that the earlier a problem is identified, the cheaper it is to fix. Applying this logic to dust control, it makes sense to tackle the source of dust instead of just cleaning up after it.
Since the transported material itself can’t be changed, the best solution is to optimize the conveyor transfer points - the primary source of airborne dust. Water mist can help suppress dust by binding particles before they spread, but in many industries, adding moisture isn’t an option. Instead, the design of the transfer point itself should be improved.
Key factors positively influencing dust reduction include:
- Height differences at loading points: Adjusting these can help minimize material disturbance but isn't always easy to do.
- The open space between the chute and the conveyor belt construction can be sealed with a polyurethane or rubber hose (Fig. 3). A LUWITAN® hose is a thin sheet material that is flexible enough to provide a permanent seal between differently moving or vibrating parts. The thin material can be easily cut to size, tensioned by hand and clamped to metal edges welded on the sides.
- Side sealing: Rubber or polyurethane strips along the conveyor belt help prevent material loss (Fig. 4). However, fine material can still escape through small gaps, especially where the belt sags between rollers (Fig. 5). Switching from rollers to sliding or damping elements reduces belt sagging, helping contain dust and protecting the belt.
- Proper sealing materials: Side seals should be made from specialized rubber compounds. Using old conveyor belts with fabric inserts for this purpose is a bad idea, as fabric causes excessive friction and can damage the belt.
- The relaxation zone: After a transfer point, dust should have space to settle onto the belt instead of dispersing into the air. Enclosing this area with metal covers helps contain dust effectively.
SafeLoad: A Complete Dust Control Solution
Rather than implementing individual fixes, the Lutze Group offers SafeLoad, a fully enclosed transfer point that integrates all these dust control measures (Fig. 6). This modular system is designed for easy customization to fit any conveyor setup (Fig. 7). Features include:
- Double sealing curtains to contain dust at the entry and exit points.
- Metal latches to prevent dust from escaping at the back.
- Belt troughing up to 70° for superior side sealing.
- Sliding elements made of polyethylene or ceramic for reduced friction and durability.
- Anti-dust seals to close gaps between moving parts and prevent dust leaks.
Proven Performance and Expert Installation
SafeLoad has been successfully installed in many steel and gypsum plants worldwide. Each installation has provided valuable technical insights, allowing Lutze to further improve its design. Our skilled technicians handle installations efficiently, while our support team ensures smooth project execution.
With over 450 employees and 40+ locations across Europe, Lutze offers a full range of conveyor system components - including belts, rollers, pulleys, scrapers, sealing systems, and wear protection solutions. We also develop innovative solutions for material handling, noise reduction, and dust control, working closely with customers to create sustainable, long-term improvements.
By addressing dust pollution at its source, SafeLoad not only reduces health risks and maintenance costs but also improves overall production efficiency.
Free translation from article in AT Mineral Processing 06/2021 - Source: Reduce dust pollution with safe transfer points - Mineral Processing