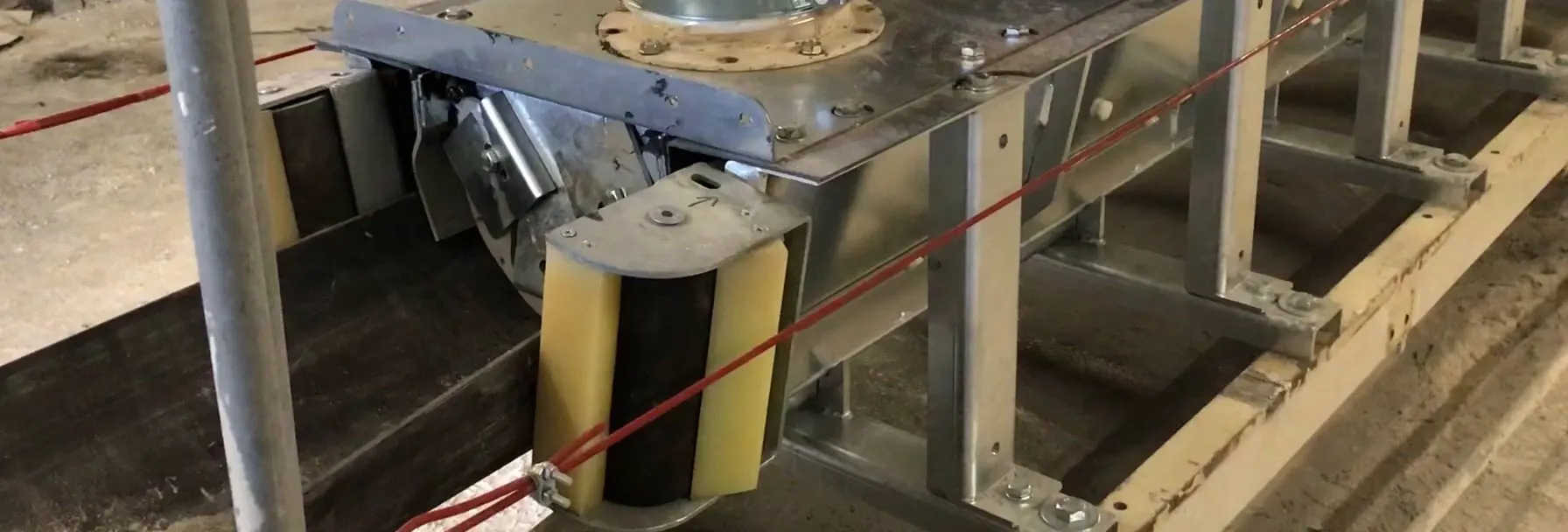
Dust Control Around Conveyor Belts
Dust control around conveyor installations
Dust control solutions employing rubber dust sealing cloths or encapsulation solutions such as our SafeLoad and Scrapetec solutions around conveyor belts and material transfer points are highly effective in mitigating the release of airborne dust particles, which can be a significant concern in various industries. Here's what you need to know about these solutions:
The aim is to create a seal along the conveyor belt and material transfer points, preventing fine particles and dust from escaping into the surrounding environment. This containment reduces the risk of health hazards to workers, minimizes material loss, and helps maintain a cleaner workspace.
- Improved Safety: Airborne dust is a safety hazard and can lead to respiratory issues and reduced visibility. Implementing dust control solutions enhances safety by reducing these risks.
- Environmental Compliance: Many industries are bound to strict environmental regulations regarding dust emissions. Employing dust sealing solutions helps operations remain compliant with these regulations, avoiding potential fines and legal issues.
- Material Conservation: By containing and recapturing dust, these solutions also prevent material loss, which can be particularly valuable in industries where materials are expensive or in limited supply. At the same time, having less or no more dust around your installations reduces cleaning costs.
- Equipment Protection: Dust is in many cases abrasive and harmful to your equipment. Dust sealing solutions can help extend the life of machinery by reducing dust-induced wear and tear.
- Customization: Dust sealing solutions can be tailored to your specific requirements and material being handled. They come in various designs and configurations to accommodate different applications.
To solve dust issues around conveyor installations, the Lutze Group offers quite many different solutions:
- SafeLoad dust encapsulation station for conveyors
- Dust sealing cloths with grip strips for screening and crushing machines, conveyor troughs, telescopic chutes, mobile systems and many more
- Conveyor installation covers for a multitude of applications
- LUWITAN® hoses and funnels for material discharge areas
LUCON SafeLoad station
A modular dust-tight belt feeding station
Our in-house developped SafeLoad system, is a modularly constructed and dust-tight feeding station, available in standard modules of 2m long.
With the following special options can make our SafeLoad fully optimized for your specific application:
- Idlers eventually equipped with buffer rings
- Impact bars
- Sliding plates with or without ceramic coating
- Stainless steel construction
Features:
- Modular construction with high variability
- Simple and minimal maintenance
- Implementable even in existing feeding stations
- Exact central positioning of the conveyed material
- Heavy and reliable construction
- Reinforced guiding rollers at feed and outlet side
- Also version for very abrasive goods
For whatever application a SafeLoad can be used in, we can customize it the way you want. The system has meanwhile proven many customers to be working perfectly inside the gypsum and chemical industry, at glass recycling plants, sand and gravel sites, steelworks and aluminum smelters.
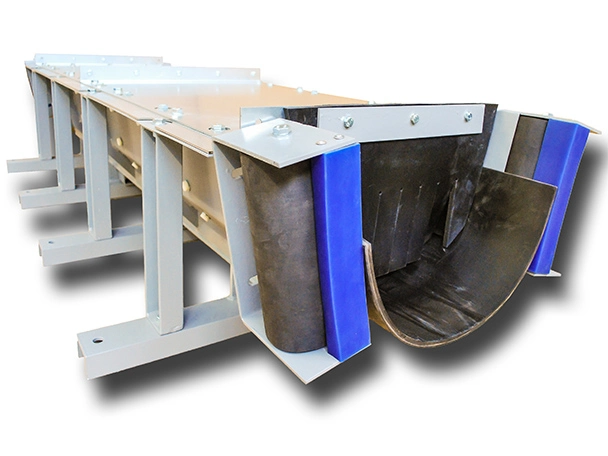
SafeLoad - a modular dust free conveyor belt feeding station
LUWITAN® hoses and hoppers
Hoses made from LUWITAN® are particularly resistant to wear and tear. We have developed a technique for homogenously manufacturing the necessary seams, without including any of the weak points such as occur with adhesive bonding or mechanical joints. The product palette includes small hoses that allow critical materials to be conveyed without dust, hoppers and hoses for filling truck concrete mixers, and hoses with diameters of several metres used for reducing dust emissions when dropping bulk material onto heaps.
Advantages
- Wear-resistant
- Oil-resistant
- High flexibility
- Outstanding form stability
- Weather-resistant
- High resistance to cuts and tearing
- Material being conveyed does not adhere to the hose
Properties
- Material hardness 65-90 Shore A
- Layer thickness 2-15 mm
- Tension reinforcement insert at points with high stresses
- Fittings as per customer request/CAD data
- Precision cut to specified dimensions in our own water-jet cutting facility
Is dust a challenge you want to get rid of?
Contact us today so we can check together what can be done!