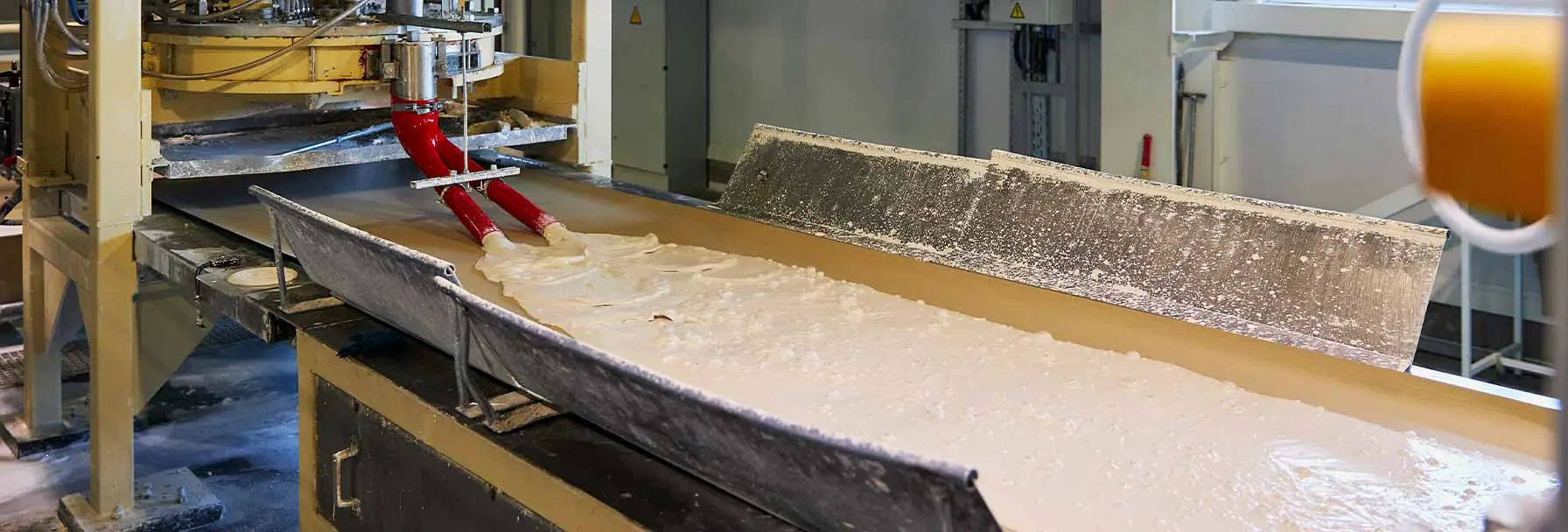
LUCON Setting Belts
Belts specifically made for the wallboard production gypsum industry
Our rubber setting belts, made for the plaster industry, have been established on the market for 40 years and complete our comprehensive range of conveyor belts. The new generation, developed in close collaboration with the wallboard industry, is used all over the world.
LUCON Setting belts installation, service and maintenance
Many of our setting belts have been installed worldwide and always under the watchful eye of our supervisors or by our own service technicians. These are connected in open lengths to perfectly fit your continuous conveyor system(s) on site. Any new belts are always subject to thorough quality inspection process before they are shipped to the customer sites as we know that these belts have to be perfect in order to produce perfect plasterboard panels.
For setting belts which are already operating, we are offering different kind of reparations in case of possible damages, enabling further high-quality wallboards production. We are offering strong technical support which means inspecting wallboard production line in total (conveyor and conveyor accessories, setting belt) and make recommendations for improvement’s. New belts are inspected and approved in our facilities in Einbeck. Customers are very welcome to join us during the final belt inspection.
We understand that these processing belts are more sensitive than conventional conveyor belts and have trained our employees accordingly. We have already convinced the majority of the European gypsum industry with our products and services.
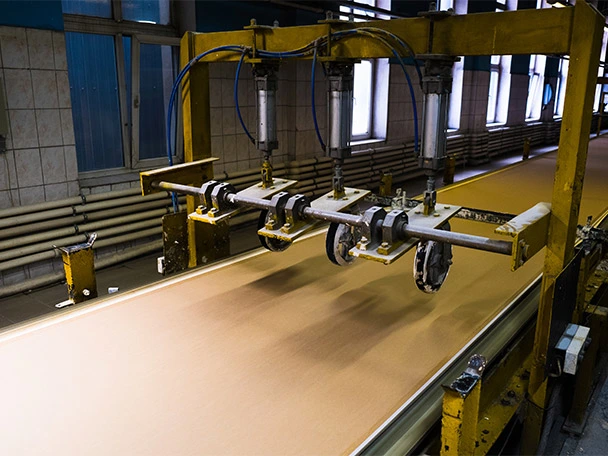
With over 40 years of experience in this segment, we are offering to the market rubber setting belts and knowledge of installation, splicing and technical support on the highest possible level.
High quality setting belts
The rubber covers of our setting belts are made of high-quality, specially developed, with non-marking and non-staining effect, light-colored Natural Rubber based rubber compound. Our setting belts are vulcanized through a continuous process.
This guarantees a seamless belt surface and eliminates heating transitions, which arise during classical vulcanisation. The established assembly results in minimal stretching and prevents the belt edges from rising up, offering our customers consistent production quality. A low friction coefficient between the belt surface and wallboard paper is achieved from beginning of the operation.
High-quality cutting machines guarantee precise straight-line processing. A complete quality assessment of the rubber cover is always carried out, after completing the conveyor belt. Many of the LUCON setting belts we have installed are still successfully performing even after 20 years in operation. These long lifetimes prove that we deliver the highest quality setting belts and splices.
In-house visual quality inspection
All setting belts we send to our customers are always subject to a visual inspection. The belts are checked for anomalies on the covers and correct thickness and hardness are controlled on multiple spots over its complete length. A detailed report is then made and sent to the customer.
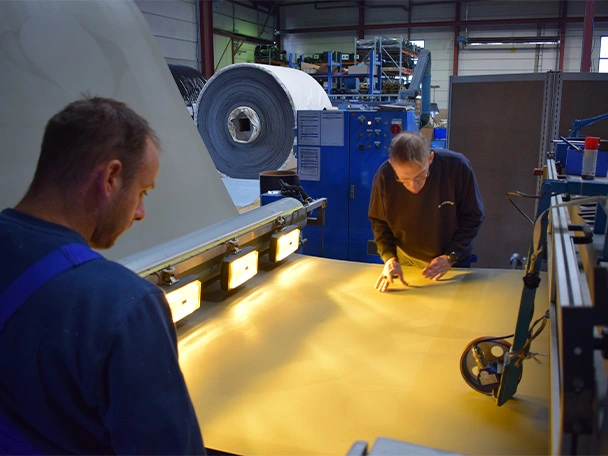
Setting belt properties
0
EP (polyester/polyamide) fabric layers, moisture resistant carcass
780
Minimum tensile strength (N/mm)
1504
Belt width up to (mm)
40
Temperature of transported material from 0°C up to
0
Belt nominal thickness +/- (mm)
45
Minimum ShA rubber cover hardness
Our setting belt specialist
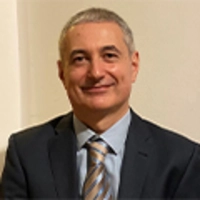
Product Application Manager
Setting Belts
Contact us for any questions related to plasterboard belts